Flexibility is the key
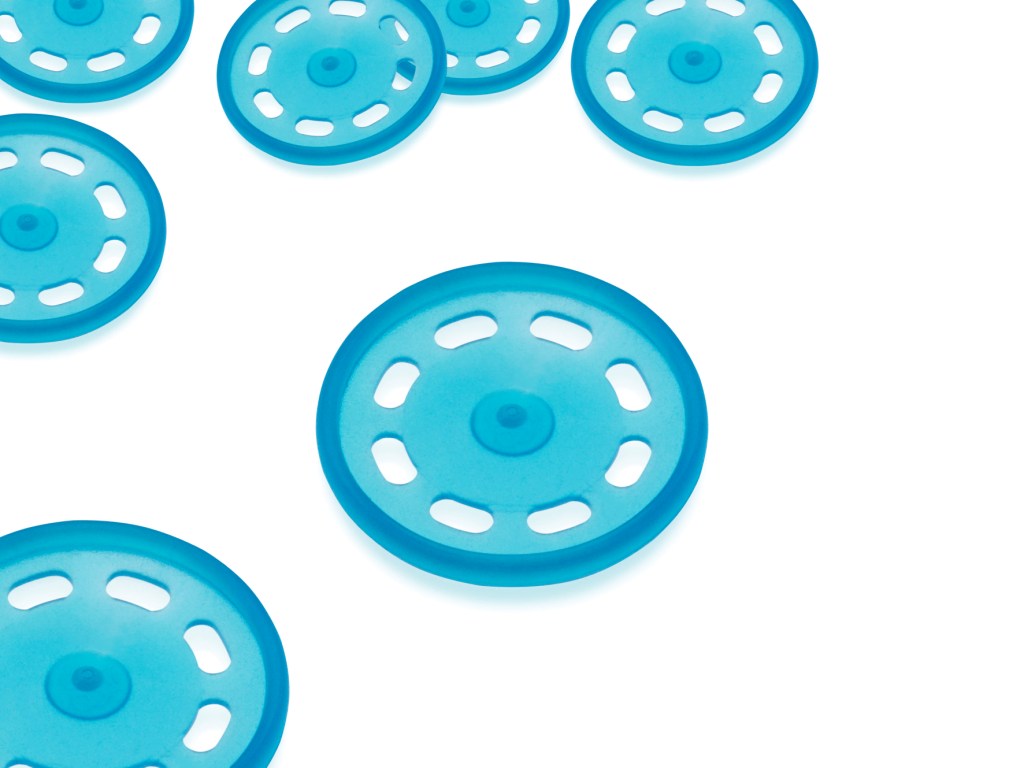
“The new PX series from KraussMaffei combines the advantages of an all-electric injection molding machine with maximum modularity in a way that is unprecedented. Our customers benefit from high precision, productivity and flexibility in all phases of production,” says Dr. Hans Ulrich Golz, President of the Injection Molding Machinery segment at the KraussMaffei Group and Managing Director of KraussMaffei. With five PX machines running at the trade show booth, KraussMaffei is highlighting customized solutions for a wide variety of applications and industries with many equipment options.
PX 50-55 SilcoSet – micro-injection molding with LSR
Extremely small shot weights, but large platens: the modular concept of the PX performs exceptionally well when processing silicone, and any PX can be retrofitted to enlarge the footprint. A 32-cavity mold creates lightweight membranes from LSR that weigh just 0.03 g, a typical application for micro-injection molding. The new PX offers particularly high precision, making it ideal for applications in medical technology. The new APC plus function thus compensates for the batch fluctuations commonly encountered when processing LSR. The ejector has an electrical and enclosed design and the automation system with a six-axis robot ensures accurate demolding of the 32 micro-components, which are then unloaded and dispensed into glasses.
PX 80-540 – Standard without additional costs
“The PX 80-540 at the K trade show is a classic ‘bread and butter’ machine that is ideally suited for standard applications, without standard applications and without costly extras. The customer does not have to make an investment in unnecessary functions,” says Dr. Golz. A highlight of the trade show booth will feature manufacturing of a electrical terminal block using flameproof material. The PX features outstandingly high speed, precision and excellent accessibility for parts transport in all directions. The energy efficiency class 9+ rating underscores the intent to produce in a way that conserves resources.
PX 120-180 with servo sprue picker – the perfect partner for clean room production
The PX 120-180 on display is a perfect match for the needs of medical technology. It features enclosed lubrication, enclosed drives and an enclosed electric ejector as well as an antistatic finish that makes cleaning easier. Upon request, KraussMaffei provides assistance during the qualification and validation process (ISO 14644, GMP). In the trade show version, the PX 120 manufactures a Y-distributor for infusions made out of PMMA. The SPX 10 servo picker takes over the demolding and cavity separation within the protective housing – and is significantly faster than the pneumatic picker. The electrical gripper function works without compressed air – cutting costs and making it ideal for clean room production.
PX 160-540 with LRX linear robot – flip-tops for the packaging industry
Thin-walled parts need power during injection. The PX 160, the machine on which flip-tops are being manufactured during K, thus has a boosted injection speed of 270 mm/s. The caps are made of PP in a diameter of 28 mm and the short thread 1881 – making this a classic packaging application. The high output quantities in this area require particularly short cycle times. Therefore, the PX 160 is equipped with speed options: faster injection, faster ejection, increased torque and faster nozzle movement. The compact automation system with LRX 100 linear robot removes the covers from the mold and places them into an integrated automation unit in which they are closed. The bottom line is that this saves time and space compared to familiar solutions on the market such as in-mold closing and separate covering process. The removal gripper is 3D-printed and thus lightweight and design-optimized.
PX 200-540 – As stylish as film, but more efficient
The inductive Dynamic Mold Heating (DMH) system from Roctool (HD Plastics) creates impressive surface effects on components without any of the technical or financial effort that film decoration or finish incur. The PX 200 creates a plastic housing of fully recycled ABS with structuring in the sub-micrometer range. The light that hits it then results in different refraction effects. The inductive system also makes it possible to prevent joint lines. The new APC plus machine function also enables completely recycled ABS materials to be processed into premium quality components without scrap.
As the mobile automation cell with industrial robot proves, an automation system can be docked quickly and conveniently. It’s as easy as plug and play. The versatile solution can be moved from one machine to another and connected there without great effort.
Partner companies
Partner companies for the KraussMaffei PX exhibits at the K 2016 included: Bada AG, Borealis Polymers NV, Bose GmbH, Evonik Performance Materials GmbH, Filtertek, Gimatic Vertrieb GmbH, gwk Gesellschaft Wärme Kältetechnik mbH, MBA Polymers, motan-colortronic gmbh, ONI Temperiertechnik, Otto Männer GmbH, Reichle GmbH, Reinhardt-Technik GmbH, Rhytemper GmbH, RocTool, SensoPart Industriesensorik GmbH, SINGLE Temperiertechnik GmbH, Trelleborg Sealing Solutions Stein am Rhein AG, UNIFORM COLOR COMPANY, Weidmüller Interface GmbH & Co. KG, Wacker Chemie AG and z-werkzeugbau-gmbh.